Introduction
There are many examples in the photographs throughout this website of AUV deployment and recovery, in part because it is one of the most 'photogenic' aspects of an AUV mission. Deployment, and especially recovery, are also high-risk operations that require great care in planning and in skill and forethought in execution. This section draws heavily on the chapter 'Launch and Recovery of AUVs in Polar Regions' by Peter Stevenson in the SUT book 'Masterclass on AUV Technology for Polar Science'. While there are a number of aspects in common between deployment from, and recovery to, a ship and an ice camp they mostly have their own particular features, and so they are treated separately here. For a hybrid ship to or from an ice camp mission then both sections are relevant.
Importantly, a deployment should not be considered complete until the AUV has begun its mission proper. Faults may develop, or their existence may become obvious, immediately the vehicle enters the water, or very soon afterwards. Operators should always have plans and any necessary equipment in place to recover the vehicle immediately should a fault develop that would jeopardise the mission.
Skip ahead to Ship or Ice Camp Deployment and Recovery or our page Finding a Missing AUV.
Some drivers for effective Deployment and Recovery capability
Stevenson listed several drivers of improvements and or effectiveness of Deployment and Recovery capability. While these are applicable in all geographical settings, the additional challenges in the Polar Regions mean several of his drivers do deserve extra considerations:
• Reduce the risk of losing the AUV and associated capital equipment (e.g. docking system). An ineffective recovery system for the Polar Regions, e.g. arising from failures in the terminal homing system, or the physical capture device at an ice-camp may lead to loss of the AUV even if an ROV is available to search and attach a line.
• Increase the probability of fulfilling the mission objectives (e.g. all wanted data gathered). Failures of the deployment method or equipment may be embarrassing, may lead to reduced operational availability or down-time while repairs are undertaken but are usually of less import that failures of the recovery method or equipment with the AUV returning with its data.
• Improve the reputation of the AUV community. While science funding agencies and commercial companies recognise the increased risks of operating AUVs in the Polar Regions, there may be little patience for problems, failures or losses relatively easily addressed risks during deployment and recovery. AUV deployments in Polar Regions often catch the public's attention or may be of national strategic importance, e.g. Canada's Cornerstone project on data gathering in support of its claim to an extended EEZ.
• Improve the operational availability. Damage to the AUV sustained during launch and recovery may take significant time to repair. All the resources needed may not be to hand, especially at an ice camp, or may entail expensive unscheduled fly-ins. Damage occurring on launch that is not detected is especially of concern if the mission itself begins. There are many anecdotes of this type of damage, e.g. damage to a control fin from impact with a piece of ice, leading to reduced performance, say from increased drag, causing reduced speed or additional power consumption, or in an extreme case, steep diving and collision with the seabed.
• Reduce insurance premiums. While usually of short duration compared with a mission the deployment and recovery times can present so many additional risks that insurers have been known to require co-insurance (risk sharing) or additional premiums. Demonstrating risk-reduction measures during Deployment and Recovery may reduce premiums.
Factors to keep in mind especially for Polar missions
• Deployment - gain prior knowledge of near surface water density and the density profile. Irrespective of whether deployment is from a ship or an ice camp it is most advisable to have a thorough knowledge of the (undisturbed) surface density and density profile to inform the buoyancy and trim calculations for the vehicle. The ability to dive, to surface, or to control depth may be affected by extreme density gradients. There is a discussion with examples on the Polar Environment page.
• Recovery - homing guidance. A homing guidance system is very likely to be necessary on ship or ice camp missions unless there are special circumstances, such as extensive, and guaranteed, open water if ship-based, of if a tether is used on an AUV deployed from an ice camp. Examples of homing systems and their use are on the Homing Guidance page.
• Trials as well as operations. From the outset, the requirements specification for deployment and recovery should include consideration of the trials requirements as well as the actual operations. The needs during trials may, of necessity, be different, e.g. when trials are from a ship or boat and the end-use will be at an ice camp. Nevertheless, trials of the actual systems should be undertaken in benign environments before deployment.
Deployment and Recovery
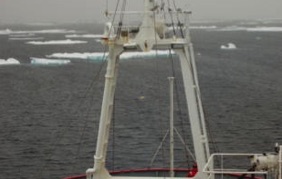

Weather conditions can change dramatically between deployment and recovery
Location: NE Greenland, August 2004.
Deployment of Autousb2 on Mission 365 on a perfect day for a 24-hour mission under fast ice toward Greenland in the far distance.
Over 24 hours, the weather changed. Visibility decreased, the wind shifted and blew in loose pack ice against the fast ice. Autosub2 is the dot between the ship's goalpost mast.
Safe recovery was helped by the homing system on Autosub. At mission end the vehicle went to a holding location- the tight loop of the blue track. Meanwhile the ship's officers found a patch of open water, the Autosub team led by Steve McPhail sent an acoustic homing signal. On receiving the signal, Autosub2 dived (red track) and set a course toward the beacon. With the team monitoring its track, a 'surface' command was sent to bring the vehicle back.

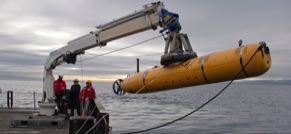
A specially-adapted crane on MBARI's RV Rachel Carson where a padded hat with a release/capture device minimises the free swing angle and maintains the AUV attitude down to,, and from, the water surface. Image courtesy MBARI educational use.
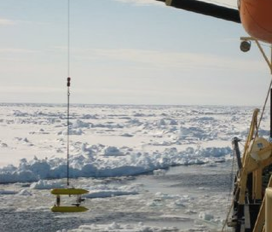
WHOI Seabed AUV crane deployment in the Arctic. A perfectly calm day, with the very long wire vertical. Only the position of the crane jib controls the location of the AUV. Image from Kunz et al. (2008).
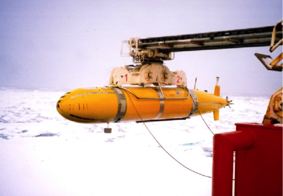
• Augmented ship's crane. There are devices under various names such as latch-head, docking head, snubber that can be fitted to the end of a ship's crane instead of a simple jib that will greatly reduce the pendulum motion. These devices are in everyday global use by the offshore ROV industry, e.g. the systems from Sepro. They are not often found for AUV deployment and recovery, and it may be no coincidence that the example opposite is from MBARI, with its long history of using scientific ROVs. The device may be hydraulically actuated to provide controlled damping of motion, to rotate the AUV, to take the AUV to the water surface and to release a latch. On recovery, the first operation would be to engage the latch, then rotate the AUV to align with the side of the ship and raise on to the deck.
Deployment from, and Recovery to, a Ship
The most common methods of AUV deployment and recovery from and to a ship are variants of methods developed over decades for offshore and oceanographic equipment.
Deployment methods from a ship include:
• Ship's crane. The path of least capital expenditure for an AUV operator is to use the equipment invariably available of a ship. This usually means a ship's crane. A major drawback with this method can be the long pendulum length between crane jib and the AUV. Even within the ice pack, long period swell can penetrate and induce the pendulum to swing. If restraining lines are used, they will be from the ship and may offer insufficient control to avoid collision with ice or the side of the ship.
