What does Mission Execution encompass?
Mission execution consists of planning the actual mission runs that the AUV will undertake, simulating them, launching the vehicle, conducting these mission runs and finally recovering the vehicle. In managing these operations, common sense, good judgement and an appreciation for local knowledge will go a long way to assuring a successful outcome.
Mission Planning and Simulation
Mission planning and simulation is becoming standard practice for AUV operations. Where a simulation capability is not available the mission plan is generally checked by an individual not involved with input to the plan. In the case of polar operations, either a simulation or an independent check (or both) help to ensure that simple program or script errors are caught before they impact on operations.
Review Fault Management Plan
In the same way, a complete review of the fault management plan is often undertaken to ensure that fail-safe actions established for surface operations are appropriate under ice. For instance, in a surface mission, a failsafe might simply consist of shutting the vehicle down and letting it float to the surface. In a polar operation, it might be more desirable for the vehicle to attempt to get back to its base, or failing that, to "park" on the sea bed if it is within the depth capability of the vehicle. Parking under the ice may be a viable option in some cases, e.g. under sea ice where the AUV is fitted with a medium frequency RF avalanche beacon. Generally, this makes it easier to locate if it is lost or disabled.
Measures to Reduce Risk in Mission Execution
In the conduct of polar operations, operators generally include one or two short, open water, missions at the start to get the feel for the local conditions and to ensure that the vehicle is essentially functional. In some cases, high risk data collection missions may be scheduled at the end of the operating period particularly if such missions are not critical to the overall success of the operation.
As the vehicle is launched it may quickly go through a large temperature change - possibly from -40 or -50C at an ice camp, to -2C or so when in water. Where there is a temperature concern, vehicles can be stored in heated tents or huts at an ice camp, or in a heated container (van) on the deck of a ship.
Ideally, missions can be planned in a manner that reduce or minimize navigational drift, that is, the difference between the true and the dead-reckoned position, even if this involves some periodic manoeuvres. At some point, however, the drift may become unacceptable and it may become necessary to update the vehicle's position.
Missions from an ice camp
In planning a an under ice mission from an ice camp the initial location will be determined by where the ice is thick enough to support the equipment involved, but thin enough to drill or cut holes. Some form of heating system is needed to keep the water in the hole from freezing over. In recovering the vehicle at an ice-hole, precise navigation is required at the end of a mission - just when the drift in the vehicle's navigation system may have reached its allowable limit. A number of operators have used an inverted USBL system in which the receiver is carried in the AUV. This allows very accurate homing to a point at which the USBL transponder is placed through a hole in the ice at the recovery location.
Best Practice for Mission Execution
Mission simulation, an independent check of the plan (or both) constitute current best practice as a means of ensuring that simple program errors are caught before they impact on operations. Prior to polar operations, the fault management plan should be reviewed in a step-by-step manner to ensure that fail-safe actions are appropriate under ice. The AUV should be fail-safed so that it will sit on the bottom rather than float to the surface.
In the conduct of polar operations, working from the simple to the difficult with high risk data collection at the end may help ensure that most data is acquired. Best practice should also involve careful planning for communications and positioning updates with the AUV.
In recovery operations, the use of an inverted USBL system should be considered to provide accurate homing.
AUV Mission Execution
Natural Resources Canada, in association with their project advisers Defence Research and Development Canada and ISE, the manufacturer of the Explorer AUV, convened a series of independently chaired workshops to review Fault Management and Mitigation. These workshops were ahead of, and between, a series of missions that gathered Arctic under ice bathymetric data in support of Canada's submission to establish the outer limits of its Arctic Ocean continental shelf. Mosher et al., 2015.
Natural Resources Canada and the project team were keen to see the methods and the results openly available and shared with the polar AUV community, Brito et al. (2012).
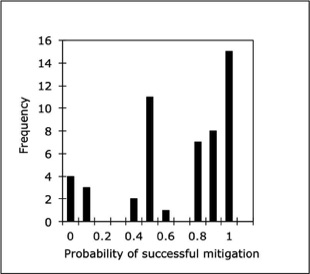
Example of independent review of the probability of successful fault mitigation prior to a polar AUV mission.
