AUV Technology
Annotated list with links to reports or papers.

Buoyancy Control
Recent concepts, developments and practical experience
Buoyancy control using hard and soft actuators
Zavislak et al. (2021) show how combining hard actuators (HA) and soft actuators (SA) can stabilize an AUV at any depth with minimum energy consumption. They develop a control algorithm to make best use of the combination of HA and SA to achieve a depth change rapidly, with minimal overshoot and to maintain a set depth with minimal excursions. Disturbance forces, for example internal waves changing the depth of isopycnal surfaces, or, in the the Polar Regions, encounters with patches of low density meltwater can be compensated.
Hard Actuators include:
• Conventional thrusters, such as electric motor-driven propellers or water jets, used either directly, e.g. as vertical or horizontal tunnel thrusters, or in conjunction with control surfaces, e.g. a motor-driven propeller at the stern in conjunction with dive planes.
• Inline motor-driven pumps that move fluid from one reservoir to another, e.g. as used in the buoyancy engines of gliders employing internal and external fluid reservoirs to alter the volume and hence density of the vehicle.
Soft Actuators include:
• The type used in the laboratory AUV in Zavislak et al.'s study - a reversible Proton Exchange Membrane fuel cell from the University of Houston. The fuel cell consumes two gasses from flexible reservoirs (exposed to the ambient pressure directly or via an intermediate working fluid) when generating electricity to reduce overall volume, or in reverse, as an electrolizer, to regenerate the gasses from the produced fluid to increase volume.
• Fully passive mechanical devices, such as the chamber with at least one rigid wall and a passively movable compensator, e.g. a spring, as in US Patent 10,640,188 B1 by Kaeli and others from WHOI.
Buoyancy control using smart materials
In his 2000 PhD thesis P. Molloy investigated three types of soft actuators for AUV buoyancy control:
• Polyacrylamide polymer gels that exhibit large volume changes with temperature and or solvent composition - for example a 200% change between exposure to saline and fresh water. However the volume change process is slow and hence of limited practical use in AUVs.
• N-isopropylacrylamide gels had a faster response, a volume change of over 800% between saline and fresh water making them a possible candidate for further study in a practical device.
• A parallel plate device was constructed with four helical Nickel-Titanium shape memory alloy springs between the plates. This was capable of exerting significant axial force, and hence a change of volume, when heated.
An energetic comparison of variable buoyancy systems for hover-capable AUVs
Carneiro et al. (2021), in a thorough and careful analysis, present important findings on the energy required by a range of different buoyancy change mechanisms. They also present a design of an optimised variable buoyancy system that had significantly lower energy requirements over existing solutions. They summarise the main advantages and disadvantages of the different families of variable buoyancy systems in a table, redrawn below.
The lower efficiency at shallow depths for hydraulic systems was very clear in their EH2b implementation, while 29.4% efficient at its maximum depth of 2100 m it was only 2.5% efficient at 100 m.
IceNode: A variable buoyancy long endurance vehicle for sub-Ice Shelf research
Clark et al. (2021) present ideas and early-stage sub-system developments for a variable buoyancy drifter with extensive situational awareness specifically designed for year long deployments under ice shelves. In part resembling a profiling float, the concept is that the vehicle, deployed at the ice front, descends, and finds / rides a current that takes it under the ice shelf. When under the shelf it may profile from seabed to the underside of the ice, e.g. for CTD+ before autonomously finding a suitable site on the underside of the ice for long-term emplacement and its task of ice-melt measurement. At the end of the mission it detaches from the ice, descends and finds a current to head into open water before telemetering its data. Emplacement may also be through a ~0.25 m hole drilled through the ice.
The concept includes acoustic sources near the ice front to provide a position-fixing capability. When under the shelf, the team propose to use a "partially observable Markov Decision Process (MDP)" using models of under ice currents and their uncertainty. In a simulation they were able to deliver 88.8% of a cluster of IceNodes to the grounding line, a 262% improvement over the unguided case, Rossi et al. (2021).
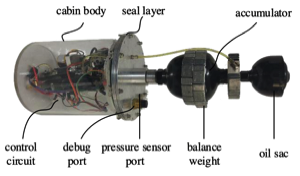
Example of a variable buoyancy mechanism and controller for a small AUV from Qiu et al. (2018).
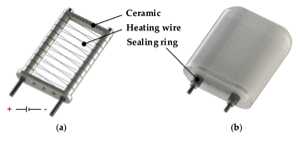
One example of a class of buoyancy change devices that use electrical energy to heat a material that expands significantly, in this case paraffin. Such devices are most applicable for for small AUVs, this example from Hou et al. (2020).
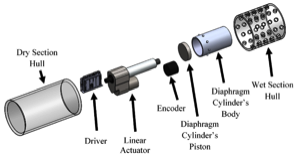
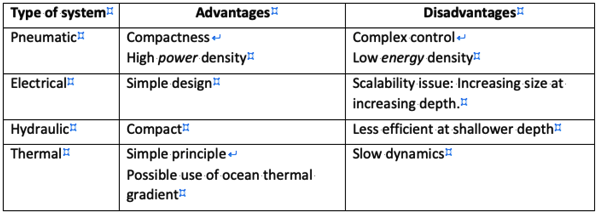
Diagram of the electrical variable buoyancy system described in Carneiro et al. (2021). For a practical system, for which they give details of the components, this system had an efficiency of 23% at 100 m, its maximum depth, occupied about 1.7 litres and was the lowest-cost solution.
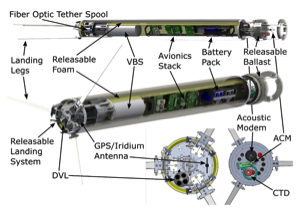
Outline diagram of IceNode, a variable buoyancy system proposed for year-long observations of basal melting of ice shelves. In operation the vehicle travels vertically, drifting in and out on sub-ice shelf currents, emplacing itself under the ice when making its measurements. From Clark et al. (2021).